8 Types of Plastic Materials Suitable for Extrusion
- Written by The Chronicle
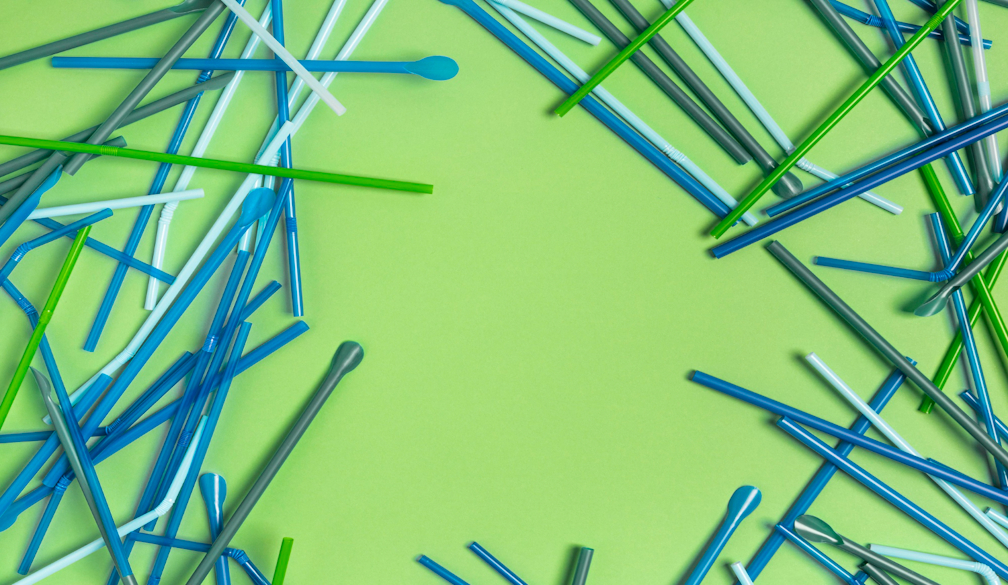
Plastic extrusion is a widely used manufacturing process that involves melting raw plastic material and forming it into a continuous profile. This process finds applications in various industries, including construction, packaging, automotive, and electronics. The versatility of plastic extrusion lies in its ability to handle different types of plastic materials. Here are eight types of plastic materials commonly used in extrusion processes:
1. Polyethylene (PE):
Polyethylene is one of the most common types of plastic materials used in extrusion. It comes in various forms, including high-density polyethylene (HDPE) and low-density polyethylene (LDPE). HDPE is known for its strength and rigidity, making it suitable for applications such as pipes, bottles, and containers. LDPE, on the other hand, offers flexibility and is often used in packaging films and tubing.
2. Polyvinyl Chloride (PVC):
PVC is a versatile plastic material that is widely used in extrusion due to its durability, chemical resistance, and affordability. It is commonly used in the construction industry for making pipes, window profiles, and siding. PVC extrusions can also be found in electrical conduits, automotive parts, and healthcare products.
3. Polypropylene (PP):
Polypropylene is a thermoplastic polymer known for its high melting point and excellent chemical resistance. It is commonly extruded into sheets, films, and fibers for packaging, textiles, and automotive applications. PP extrusions are lightweight, durable, and resistant to moisture, making them suitable for a wide range of industrial and consumer products.
4. Polystyrene (PS):
Polystyrene is a rigid and transparent plastic material commonly used in extrusion for making foam boards, packaging materials, and disposable utensils. Extruded polystyrene (XPS) foam boards are used as insulation in construction, while PS sheets are used in signage, displays, and protective packaging.
5. Acrylonitrile Butadiene Styrene (ABS):
ABS is a tough and impact-resistant plastic material commonly used in extrusion for manufacturing pipes, automotive parts, and consumer goods. It offers a good balance of strength, rigidity, and machinability, making it suitable for applications that require durability and dimensional stability.
6. Polycarbonate (PC):
Polycarbonate is a transparent thermoplastic known for its high impact resistance and optical clarity. It is commonly extruded into sheets and profiles used in construction, automotive glazing, and electronics. PC extrusions offer excellent UV resistance and flame retardancy, making them suitable for outdoor and high-temperature applications.
7. Nylon (Polyamide):
Nylon is a versatile synthetic polymer known for its strength, toughness, and abrasion resistance. It is commonly extruded into fibers, filaments, and tubes used in textiles, automotive components, and industrial machinery. Nylon extrusions offer high mechanical properties and chemical resistance, making them suitable for demanding applications.
8. PET (Polyethylene Terephthalate):
PET is a lightweight and transparent plastic material commonly used in extrusion for making bottles, containers, and packaging films. It offers excellent barrier properties against moisture and gases, making it suitable for food and beverage packaging. PET extrusions can also be found in fibers for textiles and engineering applications.
The Plastic Extrusion Process:
The plastic extrusion process involves feeding raw plastic material into a heated barrel where it is melted and forced through a die to create a continuous profile of the desired shape. The extruded plastic is then cooled and solidified before being cut to the desired length. This process allows for the production of complex shapes and profiles with consistent dimensions and properties.
Conclusion
Plastic extrusion is a versatile manufacturing process that can accommodate a wide range of plastic materials, each with its unique properties and applications. By understanding the characteristics of different plastic materials, manufacturers can choose the most suitable option for their extrusion needs, ensuring high-quality and cost-effective production.